First. rubber-coated roller product introduction:
Glued roller is an important part of the belt conveyor transportation system, the roller can effectively improve the operating condition of the conveyor system, protect the metal roller from wear and tear, prevent the conveyor belt from slipping, so that the roller and the belt synchronous operation, the roller can also be used to prevent the sliding friction between the roller and the belt to reduce the material adhesion on the surface of the roller, so as to reduce the belt deflection and wear and tear.
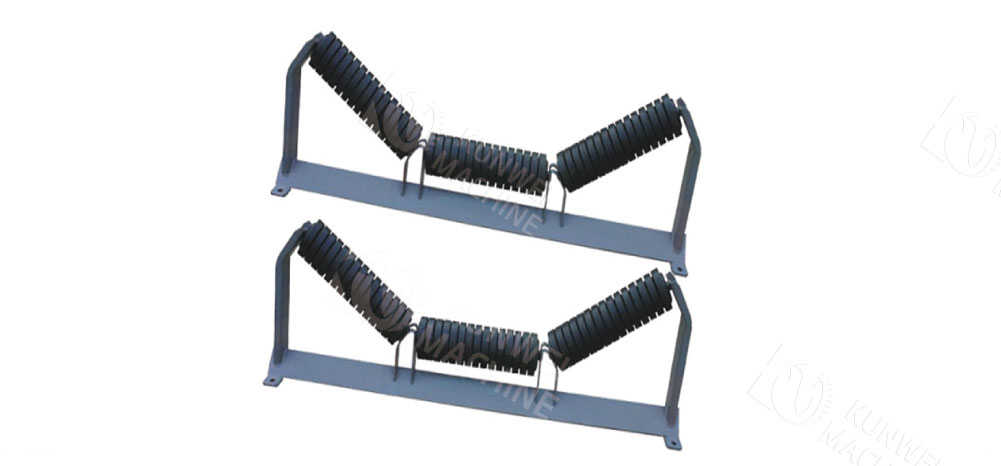
Second. rubberized roller technical parameters:
1, roller diameter: 25mm, 32mm, 38mm, 42mm, 50mm, 57mm, 60mm, 76mm, 80mm, 89mm.
2, the choice of roller material: carbon steel galvanized, carbon steel chrome-plated, carbon steel covered with rubber, aluminum alloy, stainless steel, ABS and so on.
3, the choice of roller type: powerless roller, single chain roller, double chain roller, & ldquo;O & rdquo; belt roller, conical roller, grooved roller.
4、Roller fixing method: spring press-in type, inner tooth shaft type, full flat tenon type, through-axis pin hole type.
5, rubber material can be natural rubber, nitrile rubber, neoprene rubber, EPDM rubber, polyurethane and so on.
6, rubber vulcanization bonding mode: cold vulcanization bonding mode and hot vulcanization bonding mode.
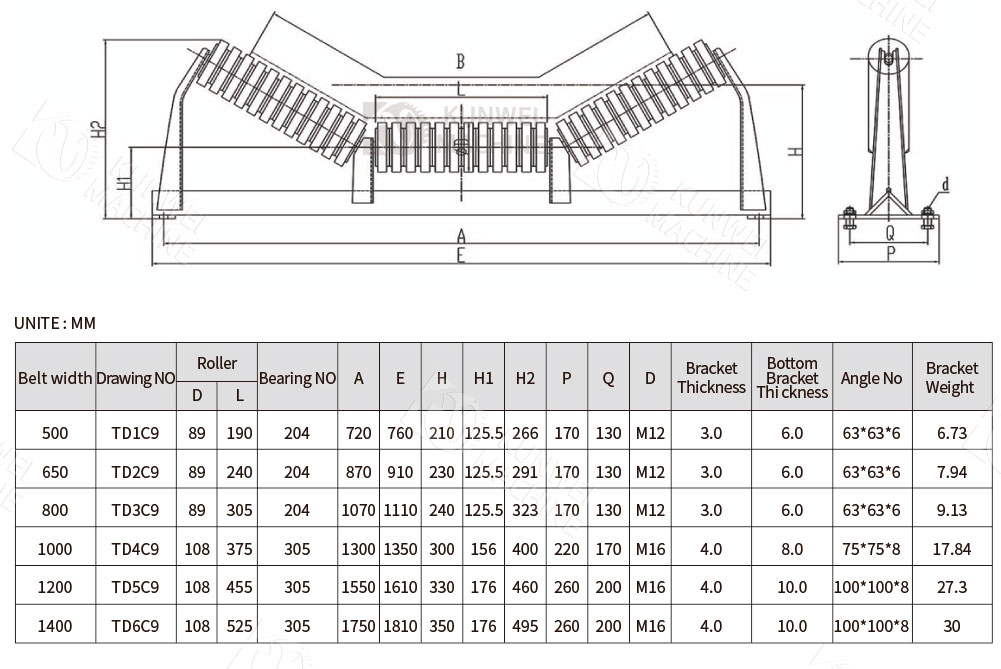
Third. the influence factors of the quality of rubber-coated roller:
1, the quality of rubber.
2, the use of rubber covering technology, rubber covering technology has hot vulcanization rubber covering and cold vulcanization rubber covering, but the mainstream of the market has been hot vulcanization process has been replaced by cold vulcanization process.
3,Construction process, the degree of skill of the adhesive coating workers also have a certain impact on the quality of adhesive coating; 4、The engineers of the adhesive coating company have a good understanding of the quality of adhesive coating.
4,The engineers of the rubber covered company analyze and deal with different conditions.
Fourth. the rubberized roller common problems and maintenance:
As the rubber-coated roller for the metal material, in the production process by vibration impact and other composite forces, will lead to roller bearing bit wear and other failures. For conveyor belt roller repair, the traditional methods of surfacing, thermal spraying, brush ferry, etc., but there are drawbacks: the thermal stress generated by the high temperature of the patch welding can not be eliminated, easy to cause damage to the material, resulting in bending or fracture of the parts; and brush plating by the thickness of the coating is limited, easy to flake off, and the above two methods are coated with metal, can not change the & ldquo; hard to hard & rdquo; the fit relationship between the forces combined. Under the combined effect of the forces, it will still cause the rubberized roller to wear again. The polymer composite material method, which has the adhesive force, excellent compressive strength and other comprehensive performance, can be free of disassembly and machining. Neither welding thermal stress, thickness is not limited, while the product has the flexibility of metal materials do not have, can absorb the impact of equipment vibration, to avoid the possibility of wear again. Roller use longer is a local breakage, the overall lining time and cost is larger, you can use cold vulcanization repair system on-site repair.
Fifth.the scope of application of rubber-coated roller:
Rubber-coated roller is widely used in: steel, metallurgy, coal, cement, power generation, fertilizer, port and other industries.